Brick by Brick
Brickworks is using waste materials from other sectors along with energy-efficient logistics chains to achieve the seemingly impossible: carbon-neutral bricks.
Sometimes, old is new. Bricks have been used since 7000BC to build homes, but the heat-intensive process typically requires large amounts of energy to be burned, adding to carbon budgets.
At its Longford facility near Launceston, Tasmania, Austral Bricks, majority owned by Brickworks, is producing Australia’s first carbon-neutral bricks to be certified under the government’s National Carbon Offset Standard.
How did it achieve this goal? The biggest step forward came by replacing the gas in its Longford brick kilns with biomass (sawdust), a by-product of the local Tasmanian timber industry. By using sawdust instead of gas, the process releases 271 tonnes of carbon dioxide a year, compared to 10,700 tonnes that the gas-led firing process would.
To put the figures into perspective, 271 tonnes is roughly the same amount of carbon dioxide that 34 households would produce annually.
Cathy Inglis, Brickworks’ General Manager of Technical and Innovation, says, “In addition to burning sawdust in its brickmaking kilns, the Longford facility has introduced a host of new measures to reduce energy in manufacturing, transport, packaging and waste to ensure the plant is more efficient.”
However, this still leaves the remaining 271 tonnes of carbon dioxide that the process is responsible for. Brickworks buys carbon offsets to make up this difference, ensuring the bricks are carbon neutral.
Carbon offsets involve a trade: essentially, the company is paying a third party to reduce carbon through projects that preserve forests and for clean energy projects.
“There is a small cost involved in buying carbon credits,” Inglis says, “but the business is able to absorb this so there is no additional cost to customers.”
Sustainability as a goal
There are numerous benefits to businesses thinking sustainably about how they manufacture: marketplace positioning, cost reduction, resource saving, and as a broader avenue for innovation.
The changes at Brickworks’ Longford plant are part of a wider commitment that Brickworks has to making its Australian operations cleaner, greener and more efficient, with 50,000 tonnes year in carbon dioxide emissions in the firing line.
For its other gas-fired kilns, the company is sourcing landfill gas from energy providers that would otherwise have been burnt off and wasted, while new fuels built from commercial, industrial, demolition and green wastes are being trialled as replacements.
It is even rethinking the chemical compositions of its bricks, introducing biosolids from alternative sources into the brick mixture to create lighter bricks that save energy in the manufacturing process, and in transportation.
Ric West, Commercial Analyst for Austral Bricks Victoria, says, “Fortunately, there is no extra cost in carbon-neutral bricks and they are delivered carbon neutral to site anywhere in the world,” he says. “So it’s a win-win for the homeowner and the environment.”
This article is taken from the recently published digital book
Australia's Nobel Laureates Vol III State of our Innovation Nation: 2021 and Beyond
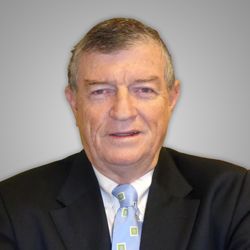